FMP 211 :: Lecture 17 :: TRACTOR AND IMPLEMENT SELECTION FOR DIFFERENT AGRICULTURAL OPERATIONS
Putting together an ideal machinery system is not easy. Equipment that works best one year may not work well the next because of changes in weather conditions or crop production practices. Improvements in design may make older equipment obsolete. And, the number of acres being farmed or the amount of labor available may change. Because many of these variables are unpredictable, the goal of the good machinery manager should be to have a system that is flexible enough to adapt to a range of weather and crop conditions while minimizing long-run costs and production risks
POINTS TO BE CONSIDERED IN SELECTING A FARM MACHINERY
To do better farm machinery selection, the following fundamental things must be understood
1. Machine Performance
Each piece of machinery must perform reliably under a variety of field conditions or it is a poor investment regardless of its cost. Tillage implements should prepare a satisfactory seedbed while conserving moisture, destroying early weed growth and minimizing erosion potential. Planters and seeders
should provide consistent seed placement and population as well as properly apply pesticides and fertilizers. Harvesting equipment must harvest clean, undamaged grain while minimizing field losses. The performance of a machine often depends on the skill of the operator, or on weather and soil conditions. Nevertheless, differences among machines can be evaluated through field trials, research reports and personal experience.
2. Machinery Costs
Once a particular type of tillage, planting, weed control, or harvesting machine has been selected, the question of how to minimize machinery costs must be answered. Machinery that is too large for a particular farming situation will cause machinery ownership costs to be unnecessarily high over the long run; machinery that is too small may result in lower crop yields or reduced quality.
3. Ownership Costs
Machinery ownership costs include charges for deprecation, interest on investment, property taxes, insurance and machinery housing. These costs increase in direct proportion to machinery investment and size.
4. Operating Costs
Operating costs include fuel, lubricants and repairs. Operating costs per acre change very little as machinery size is increased or decreased. Using larger machinery consumes more fuel and lubricants per hour, but this is essentially
offset by the fact that more acres are covered per hour. Much the same is true of repair costs. Thus, operating costs are of minor importance when deciding what size machinery is best suited to a certain farming operation
5. Labor Cost
As machinery capacity increases, the number of hours required to complete field operations over a given area naturally declines.
6.Estimating the Field Capacity of Farm Machines
If hourly or part-time hired labor operates machinery, it is appropriate to use the wage rate paid, plus the cost of any other benefits which may be provided, as the labor cost. If the farmer-owner or a hired worker who is paid a fixed wage operates machinery, then it is proper to value labor at its opportunity cost, or the estimated return it could earn if it were used elsewhere in the farm business, such as in livestock enterprises.
7. Timeliness Costs
In many cases, crop yields and quality are affected by the dates of planting and harvesting. This represents a “hidden” cost associated with farm machinery, but an important one nevertheless. The value of these yield losses is commonly referred to as “timeliness costs.”
8. Total Machinery Costs
Illustrates the effect that changes in machinery size have on each type of cost in a typical situation. For very small machinery (relative to crop acres), a slight increase in machinery size can lower timeliness and labor costs significantly, enough to more than offset the higher fixed costs. However, as machinery size continues to increase, the timeliness cost savings diminish, and eventually total costs begin to rise. One objective of machinery selection, then, is to select machinery in the size range where total machinery costs are lowest.
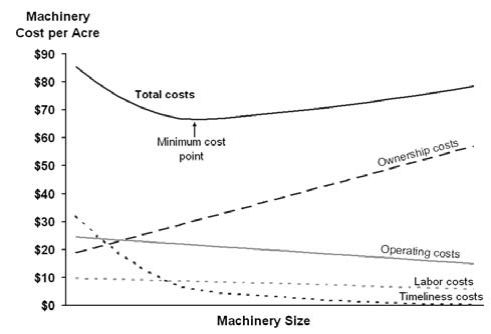
Fig1. Effect of increasing machinery size on machinery costs.
FACTORS THAT AFFECT THE SIZE OF MACHINERY NEEDED
Machinery recommendations must be based on the characteristics of each individual farm. The following factors influence machinery selection, and are discussed in order of importance.
1. Number of Crop Acres
As more crop acres are farmed, larger-scale machinery is needed to ensure that planting and harvesting are completed in a timely fashion. An alternative is to acquire a second unit of some machines, if an additional tractor and operator are available.
2. Labor Supply
The number of acres that can be completed each day is the most critical measure of machinery capacity, more than machine width or acres completed per hour. Increasing the labor supply by hiring extra operators or by working longer hours during critical periods may be a relatively inexpensive way of stretching machinery capacity. In addition, the cost of additional labor only needs to be incurred in those years in which it is actually used, while the cost of investing in larger machinery becomes “locked in” as soon as the investment is made. On the other hand, extra labor may not always be available when needed, and working long hours over several days can present a safety hazard.
3. Tillage Practices
The number of field days needed before planting is completed depends partly on the number of separate operations completed on each acre. Reducing the number of tillage practices performed or performing more than one practice in the same trip effectively decreases the amount of machinery capacity needed to complete field operations on time. Of course, machinery cost savings from reduced tillage must be compared to possible increased chemical costs and effects on yields.
Putting together an ideal machinery system is not easy. Equipment that works best one year may not work well the next because of changes in weather conditions or crop production practices. Improvements in design may make older equipment obsolete. And, the number of acres being farmed or the amount of labor available may change. Because many of these variables are unpredictable, the goal of the good machinery manager should be to have a system that is flexible enough to adapt to a range of weather and crop conditions while minimizing long-run costs and production risks
POINTS TO BE CONSIDERED IN SELECTING A FARM MACHINERY
To do better farm machinery selection, the following fundamental things must be understood
1. Machine Performance
Each piece of machinery must perform reliably under a variety of field conditions or it is a poor investment regardless of its cost. Tillage implements should prepare a satisfactory seedbed while conserving moisture, destroying early weed growth and minimizing erosion potential. Planters and seeders
should provide consistent seed placement and population as well as properly apply pesticides and fertilizers. Harvesting equipment must harvest clean, undamaged grain while minimizing field losses. The performance of a machine often depends on the skill of the operator, or on weather and soil conditions. Nevertheless, differences among machines can be evaluated through field trials, research reports and personal experience.
2. Machinery Costs
Once a particular type of tillage, planting, weed control, or harvesting machine has been selected, the question of how to minimize machinery costs must be answered. Machinery that is too large for a particular farming situation will cause machinery ownership costs to be unnecessarily high over the long run; machinery that is too small may result in lower crop yields or reduced quality.
3. Ownership Costs
Machinery ownership costs include charges for deprecation, interest on investment, property taxes, insurance and machinery housing. These costs increase in direct proportion to machinery investment and size.
4. Operating Costs
Operating costs include fuel, lubricants and repairs. Operating costs per acre change very little as machinery size is increased or decreased. Using larger machinery consumes more fuel and lubricants per hour, but this is essentially
offset by the fact that more acres are covered per hour. Much the same is true of repair costs. Thus, operating costs are of minor importance when deciding what size machinery is best suited to a certain farming operation
5. Labor Cost
As machinery capacity increases, the number of hours required to complete field operations over a given area naturally declines.
6.Estimating the Field Capacity of Farm Machines
If hourly or part-time hired labor operates machinery, it is appropriate to use the wage rate paid, plus the cost of any other benefits which may be provided, as the labor cost. If the farmer-owner or a hired worker who is paid a fixed wage operates machinery, then it is proper to value labor at its opportunity cost, or the estimated return it could earn if it were used elsewhere in the farm business, such as in livestock enterprises.
7. Timeliness Costs
In many cases, crop yields and quality are affected by the dates of planting and harvesting. This represents a “hidden” cost associated with farm machinery, but an important one nevertheless. The value of these yield losses is commonly referred to as “timeliness costs.”
8. Total Machinery Costs
Illustrates the effect that changes in machinery size have on each type of cost in a typical situation. For very small machinery (relative to crop acres), a slight increase in machinery size can lower timeliness and labor costs significantly, enough to more than offset the higher fixed costs. However, as machinery size continues to increase, the timeliness cost savings diminish, and eventually total costs begin to rise. One objective of machinery selection, then, is to select machinery in the size range where total machinery costs are lowest.
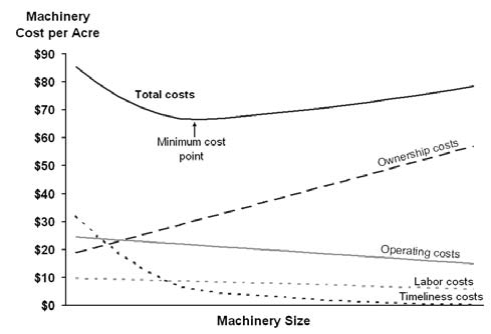
Fig1. Effect of increasing machinery size on machinery costs.
FACTORS THAT AFFECT THE SIZE OF MACHINERY NEEDED
Machinery recommendations must be based on the characteristics of each individual farm. The following factors influence machinery selection, and are discussed in order of importance.
1. Number of Crop Acres
As more crop acres are farmed, larger-scale machinery is needed to ensure that planting and harvesting are completed in a timely fashion. An alternative is to acquire a second unit of some machines, if an additional tractor and operator are available.
2. Labor Supply
The number of acres that can be completed each day is the most critical measure of machinery capacity, more than machine width or acres completed per hour. Increasing the labor supply by hiring extra operators or by working longer hours during critical periods may be a relatively inexpensive way of stretching machinery capacity. In addition, the cost of additional labor only needs to be incurred in those years in which it is actually used, while the cost of investing in larger machinery becomes “locked in” as soon as the investment is made. On the other hand, extra labor may not always be available when needed, and working long hours over several days can present a safety hazard.
3. Tillage Practices
The number of field days needed before planting is completed depends partly on the number of separate operations completed on each acre. Reducing the number of tillage practices performed or performing more than one practice in the same trip effectively decreases the amount of machinery capacity needed to complete field operations on time. Of course, machinery cost savings from reduced tillage must be compared to possible increased chemical costs and effects on yields.
ESTIMATING POWER REQUIREMENTS
Estimation of draft
In order to determine the draft requirement of an implement it is necessary to use a pull meter. Estimation of likely draft requirements can be taken from the table provided. However, these values will vary according to soil type, soil moisture, depth of working, ground speed and manufacturer.
Table 3 Estimating Draft Requirements
Implement |
Draft per Unit Width (kN/m) |
Chisel plough |
4.5-5.5 |
A figure for total draft can be calculated by simply multiplying implement width by draft per unit width. Considering the example using the chisel plough, then:
Total draft = width (m) x draft / metre (kN/m)
= 7.8 x 5
= 39 kN ( approx. 3900 kgf)
If a scarifier was used to replace the chisel plough, the draft per unit width would decrease to 4.5 kN/m and the resultant total draft would be 35 kN (3500 kgf). Remember this is draft or pull, not drawbar power.
Estimation of drawbar power
Drawbar power can be related to draft and speed, by using the formula below. Any one drawbar power level may be attained by a combination of pull and speed. That is, a large pull at a low speed could produce the same drawbar power as a small pull at high speed.
Drawbar power = pull (kN) x speed* (km/hr)
3.6 (constant)
Using the same chisel plough as in the previous example, the power requirements become:
Drawbar power = 39 x 8
3.6
= 87 kW (116hp).
*Speed has been determined by the initial assumption when working out the required implement width.
Note: Kilowatts (kW) x 1.34 = Horsepower (hp)
Horsepower (hp) x 0.746 = Kilowatts (kW)
At this point, it would pay to work through all of the tillage operations and determine the requirements for each, after closely considering the time available and field efficiency. The largest power requirement would be then used in determining engine power.
Estimating engine power
Once drawbar power has been calculated, a decision needs to be made about what type of tractor is to be used.
The selection decision between wheels or tracks is far too complex a topic to be covered in this chapter. Suffice to say that if set-up and matched correctly, the operating costs should be similar for either tractive type. The decision between two wheel drive and four wheel drive is much simpler as it is determined by the minimum available size of a 4WD and the maximum size of a 2WD (that is approximately 150 kW or 200 hp).
From Table 2, it is now possible to determine the size of tractor required. In using the comparative chart it would be unwise to determine engine size using the maximum power figure as conditions vary both from season to season and even within any one season. Having a little extra capacity is also a safeguard against overloading. A more realistic figure is the normal operation level.
Table 4: Tractor Crankshaft Power (Chisel plough example)
Tractor |
Drawbar HP/ Efficiency |
Crankshaft Power (kW) |
2WD |
(87 x 100)/40 |
=217 kW (290 hp) |
CONCLUSION
If a step by step approach is used when matching power units and implements, it is possible to eliminate the majority of guess work that is normally employed when a machinery purchase decision is made.
This approach is simplistic but does allow changes to any of the inputs. Care must be taken not to over estimate either the time available to complete the task or field efficiency.
APPENDIX
Table 1 shows estimated draft requirements for various implements
Table 1 . Default Values for Speed, Field Efficiency, and Draft Requirements.
Equipment Name | Speed (mph) |
Draft (lb. per unit of width) |
Average Range |
Tillage |
|||
Moldboard plow (16 in. bottom, 7 in. deep) |
5.0 |
320 |
220 - 430 per foot |
Chisel-plow |
5.0 |
500 |
200 - 800 per shank |
Disk |
5.5 |
75 |
50 - 100 per foot |
Field cultivator |
5.0 |
300 |
200 - 400 per foot |
Spring-tooth harrow |
5.0 |
200 |
70 - 300 per foot |
Spike-tooth harrow |
6.0 |
50 |
20 - 60 per foot |
Roller or packer |
5.0 |
100 |
20 - 150 per foot |
Cultivator |
5.0 |
250 |
60 - 300 per foot |
Rotary hoe |
7.5 |
84 |
30 - 100 per foot |
Subsoiler (16 in. deep) |
4.5 |
1500 |
1,100 - 1,800 per |
Planting |
5.0 |
5.0 |
|
Applying Chemicals |
4.5 |
425 |
375 - 450 per shank |
![]() |
Download this lecture as PDF here |